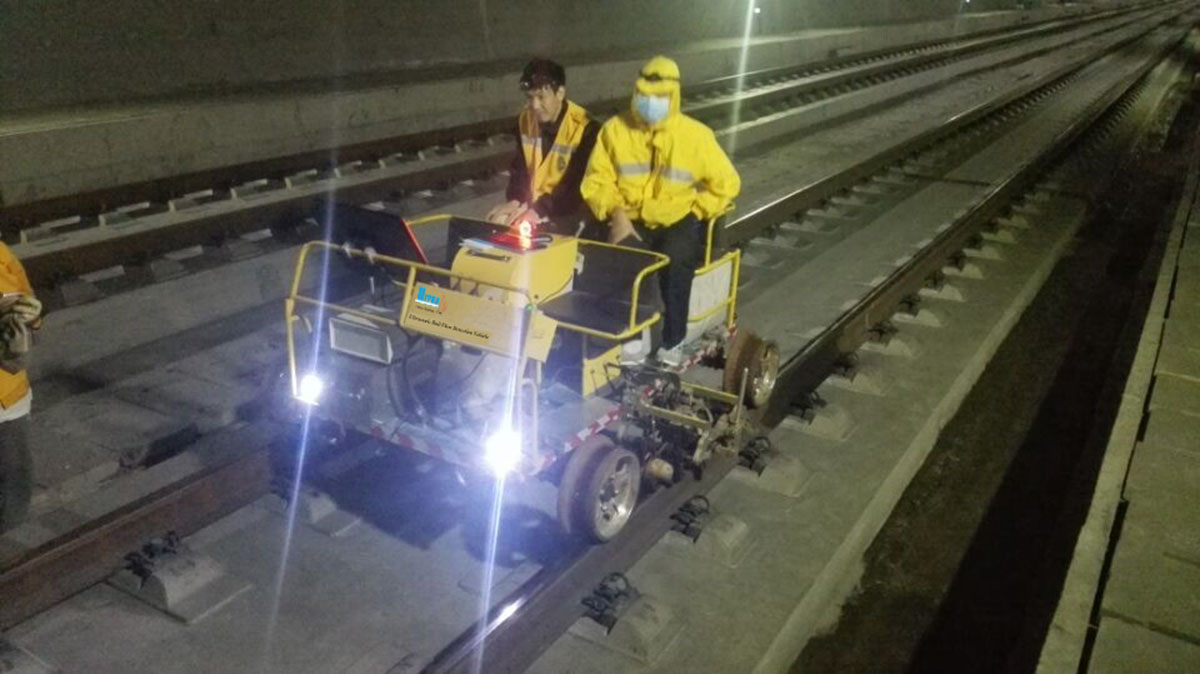
First, before the previous rail flaw detection, it is necessary to carefully and debug the performance of the instrument in all aspects. Such as the indication of voltage, the combination of rail probe and protective film. The pressure of each connecting line and probe, waterway, etc. So as to ensure that the rail instrument will not be “defective” on the track.
Second, after being on the track, it is necessary to integrate the position of each channel alarm door, the position of probe and the sensitivity of rail flaw detection according to the specific type and condition of rail.
Third, during the operation, it should strictly control the flaw detection speed to achieve “joint station, small waist slow and large waist uniform detection”. The alarm sound of each channel shall be clear enough. The waveform display of each channel shall be clear. The position of all probes on the rail shall be carefully visuable. If there is an abnormal display or alarm, repeated detection will carry out. The sensitivity and position of rail flaw detection shall be corrected in time according to the combination.
Fourth, for those staggered teeth, insulated joints, switch rails, etc., it is necessary to detect the positive and negative directions. Improve the gain and increase the water injection.
Fifth, for those positions where the rail head peels off seriously, the relevant detection instruments will fail. Therefore, it is necessary to do a variety of manual cooperation and detection. It should be in strict accordance with the operating procedures to avoid missed detection.
Sixth, according to the display process of good waveform of rail damage, multiple probes and means are to carry out and check and verify at multiple levels. Do not miss any suspicious information and location, so as to avoid accidents such as missed inspection or wrong judgment.
More Additional Explanations.
In addition, it is necessary to change the detection direction of the probe regularly every month. That is, the inner rear outer direction in single month and the outer rear inner direction in double months. For the detection of side wear track on curve, adjust it regularly. So as to reduce the blind area of track detection.