Ultrasonic flaw detection is a method to check part defects by using the characteristics of reflection at the edge of the interface, Ultrasonic energy penetrates into the depth of metal materials and enters another section from one section. When the ultrasonic beam passes from the part surface to the metal from the probe, reflected waves will occur respectively. When encountering defects and the bottom surface of parts, forming pulse waveforms on the fluorescent screen, The defect position and size are determined according to these pulse waveforms, this ultrasonic flaw detection is the best way for rail flaw detection in the world.
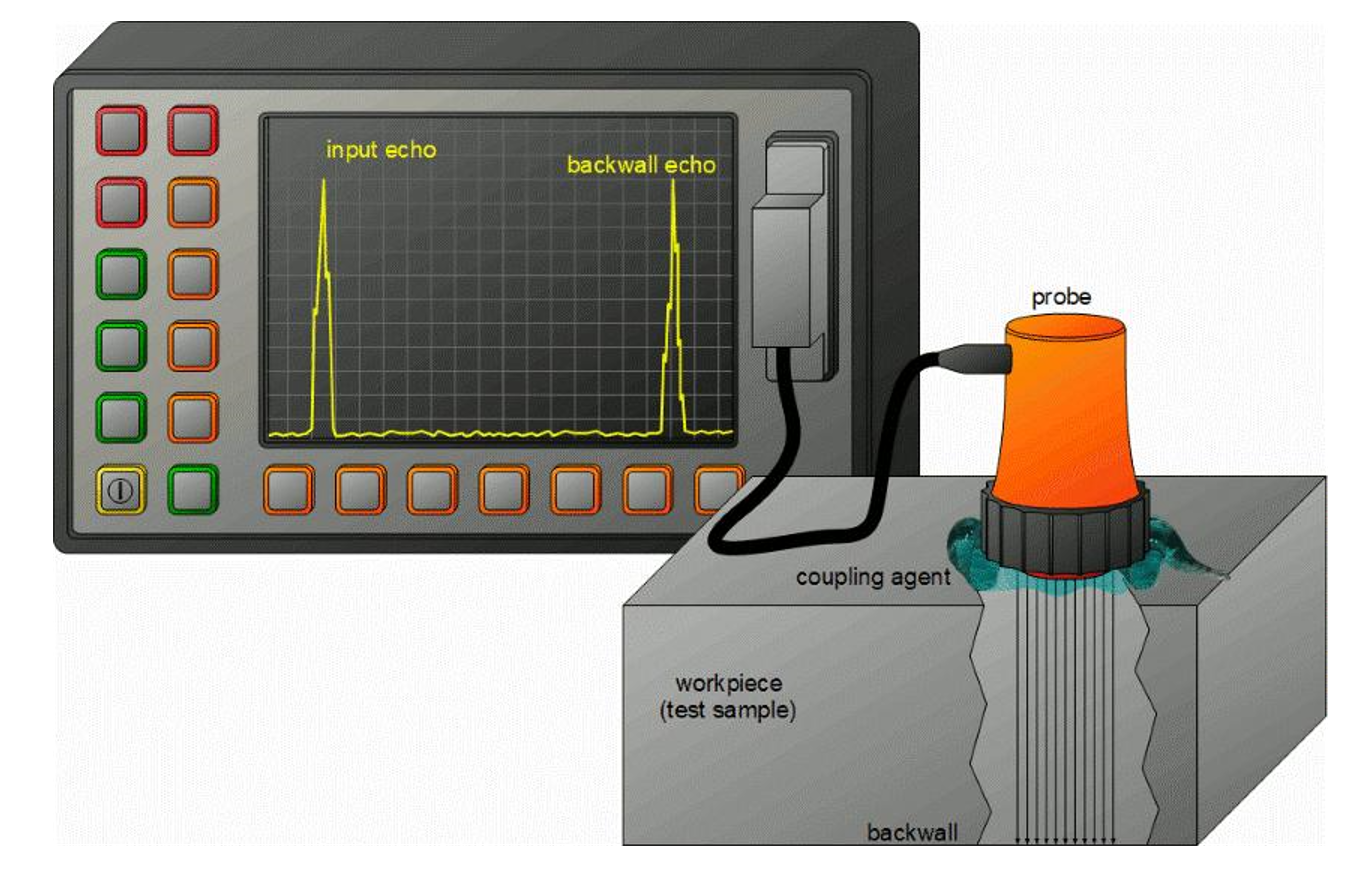
Ultrasonic Flaw Detection
Characteristic
1. When the ultrasonic wave propagates in the medium, it has the characteristics of reflection on different qualitative interfaces. If there is a defect, and the size of the defect is equal to or greater than the ultrasonic wave length. The ultrasonic wave will reflect back on the defect, and the flaw detector can display the reflected wave; If the size of the defect is even smaller than the wavelength, the sound wave will bypass the defect.
2. The wave sound has good directivity. The higher the frequency, the better the directivity. It radiates into the medium with a very narrow beam, which is easy to determine the location of defects
3. The propagation energy of ultrasonic wave is large. For example, the energy transmitted by ultrasonic wave with frequency of 1MHz (1 MHz) is equivalent to 1 million times of sound wave with the same amplitude and frequency of 1000Hz (Hz).
By Ultra Instrument Inc.