Definition of rail flaw detection vehicle: special vehicle equipped with rail damage detection equipment.
Devolopment history:the transverse crack at the rail head (commonly known as core damage) has caused many rail breaking accidents. In 1923, the American Railway Engineering Association (AREA), the rail committee entrusted Sperry company to develop testing equipment. On October 2, 1928, the company developed the world’s first rail flaw detection vehicle and began to put it into use. Since then, various types of flaw detection vehicles have entered the market for many years.
Classification: according to the testing principle of rail detection, it is divided into electromagnetic flaw detection vehicle and ultrasonic flaw detection vehicle.
The electromagnetic flaw detection vehicle detects the rail damage through the non-contact magnetic method. Its best detection speed is 30 ~ 70 km/h. This measurement method can not detect the damage of the rail waist and the joint of the rail. The best sensitivity for detecting the core damage is only 20% ~ 25%, cross-sectional area of the rail head. Because of these limitations, it is gradually replaced by the ultrasonic flaw detection vehicle.
Development History of Rail Flaw Detection Vehicle
Kraut Kramer company of Germany successfully develop the ultrasonic rail flaw detection vehicle in 1956. This vehicle uses ultrasonic to detect the vehicle, which can detect the fatigue defects and welding curves near the rail head, and waist of the rail, including the joint as well. Some can also detect scratches, rail head crushing, wavy wear, rail bottom corrosion and crescent falling. This vehicle is equipped with automatic recording instrument, which can record the damage signal of steel rail, mileage signal and line characteristic signal (bridge, tunnel, joint, sleeper type, etc.) are recorded on the same paper tape or film. According to the recorded information, the size and position of rail damage can be analyzed, and the route mileage of rail damage can also be determined. In addition, the second continuous record can also analyze the development speed and development law of rail damage.
The driving speed of ultrasonic flaw detection vehicle is 10 ~ 5 0 km/h, the best sensitivity for detecting nuclear injury is 50 mm2, and the best sensitivity for detecting rail waist crack is equivalent to a borehole with a diameter of 3 mm. The minimum error of determining the line position of rail crack is ± 10cm. Uneven or unclean rail surface will affect the detection sensitivity of such vehicles, especially the damage detection sensitivity near the joint.
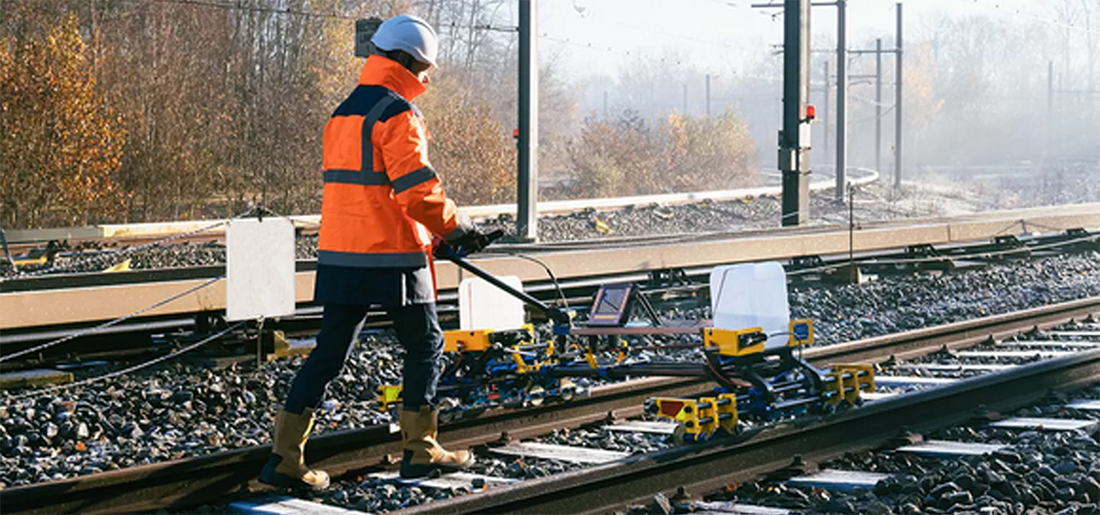
hand push rail flaw detection trolley
Development Directions of the Vehicle
In addition, small portable hand push rail flaw detection trolleys are also popular in many countries, which have a good effect. In combination with flaw detection trolleys with high automation and high speed one. To improve the technical level of detection, the product is developing in the following directions: 1. The damage signal obtained by computer processing; 2. Automatic mileage setting; 3. Improve the method of manual operation of the ultrasonic probe when entering the turnout to realize no landing or automatic landing; 4. Improve the speed and detection efficiency of the ultrasonic flaw detection vehicle; 5 Explore a more reasonable non-contact detection method.
UR18-D double rail ultrasonic flaw detection vehicle by Ultra Instrument Inc.
- Origin: USA
- Core features:
- Electric type, fast speed
- Large capacity lithium battery drive, long service life
- Non contact 9-channel ultrasonic wheel probe
- The A/B scan display at the same time. And B scan can record in real time, and the replay software realizes the detection record.
- Detachable titanium alloy chassis, quick disassembly and convenient handling.